The F-22 Raptor, a fifth-generation stealth fighter developed by Lockheed Martin, is one of the US Air Force’s flagship fighters. However, due to the completion of production in 2011, parts procurement for repair and replacement is becoming difficult. Thus, the US Air Force is targeting to produce and deliver fighter parts to metal 3D printers and is piloting the plan.
In December last year, Hill Air Force Base 574 aircraft maintenance unit in Utah, USA, installed parts made of metal 3D printers on F-22 raptors. According to the official, the F-22, which has a small size, has a smaller number of components than its predecessor, and its difficulty is getting higher every year to get parts even after the end of production. If you ask the factory for production, you have to produce more than the determined amount, so the minimum order quantity is needed and the cost goes up.
As a result, titanium powder is laminated using a metal 3D printer installed at Hill Air Force Base, and laser parts are formed. With metal 3D printers, it takes just three days to complete a new part and send it to the scene. 3D printers will save you not only time and money, but also time.
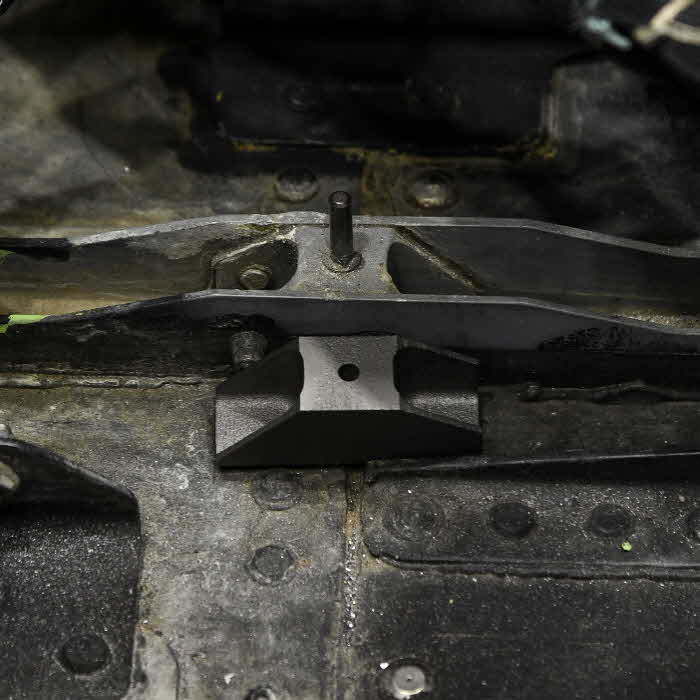
In fact, if you look at the interior of the cockpit exchanged at Hill Air Force Base, aluminum parts are said to be one of the most frequently replaced parts because of the large corrosion. At Hill Air Force Base, at least five of the F-22 components are output to a 3D printer. These 3D printer-based services will be piloted by the US Air Force to introduce metal 3D printer technology through a private partnership. A Lockheed Martin official said that if it could output more complex parts to a 3D printer, it could reduce the time it takes to repair a fighter by 60 to 70 days.
This is not the first attempt to use 3D printers in the military. In fact, the US Marine Corps is already actively applying the latest technologies, such as developing technologies to build barracks within 24 hours using 3D printers and remicon.
The US Marine Barracks had to build 10 soldiers over five days, but using 3D printers could be done within 24 hours. The 3D printer barracks are surrounded by a thin layer of concrete. Through experimentation, we made 14 pyong barrels in 40 hours.
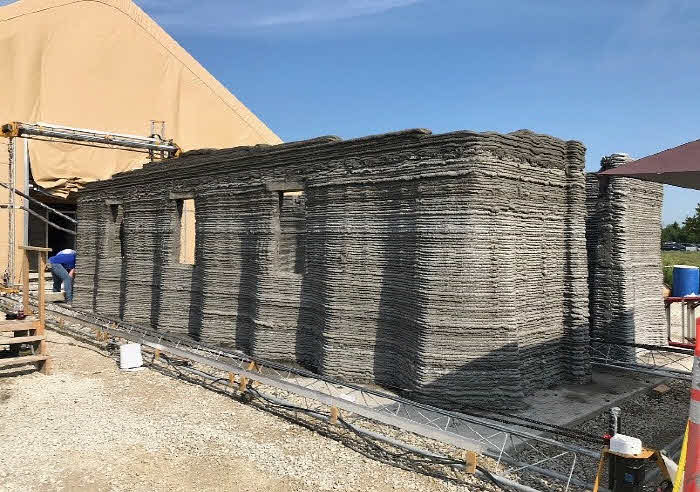
The 3D printer was controlled by a PC 10 years ago, and it took 40 hours to build it with expert inspections and concrete replenishment, but in reality it can be completed within 24 hours if only concrete replenishment machines are used. When stacked with a 3D printer, there is a gap between the walls, which can reduce the amount of concrete used. It also helps reduce carbon dioxide emissions when manufacturing.
The biggest advantage is that it can reduce manpower for construction and improve safety. Up to now, 10 soldiers have been working for 5 days and almost can be handed over to automation machines. You do not have to take risks and you can also minimize the loss of soldiers near the wires. Attempts to utilize 3D printers in the military are continuing. For more information, please click here .