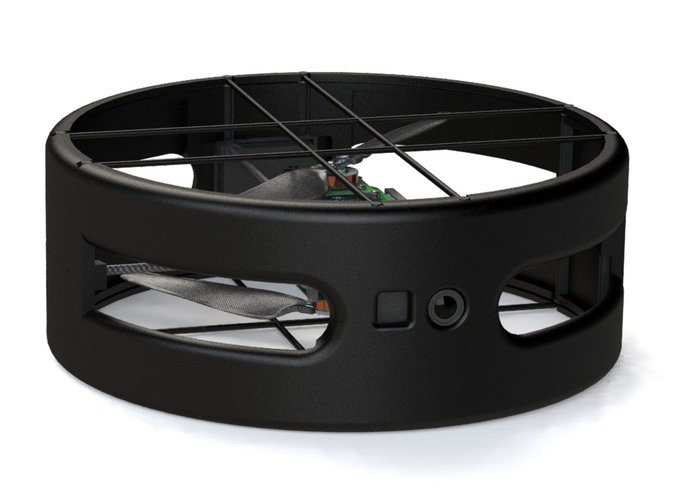
The Lausanne Federal Institute of Technology and FLYBOTIX are developing a dual-propeller drone with two-stage rotors. Most of the drones currently in use are quadcopters, meaning they float in the air using four rotating blades. The downside is that it takes a lot of power because it has four wings that rotate at once.
In contrast, dividing the rotor into two can increase the low-noise capability and double the battery life. Although the propeller shaft is made up of two stages, it is a coaxial reversing rotor method that rotates in reverse so that the drone body does not rotate.
When the propeller reaches the second stage, it is easy to imagine going up and down. But how do you move back and forth, left and right? It uses a control system developed by Flybotics. The ability to control the propeller rotation speed and inclination using an accelerometer and a gyroscope enables stable front-to-back, left-to-right flight.
Drones are suitable for inspection and monitoring in oil or gas factories, but they can also be used to secure public safety and to police agencies. The drone’s test flight took place in a location that mimics the scene of the disaster, and it also flew between steel frames. The coaxial reversing rotor is an old technology, but it is a new thing to introduce for drones that fly quietly and stably for a long time. Related information can be found here .